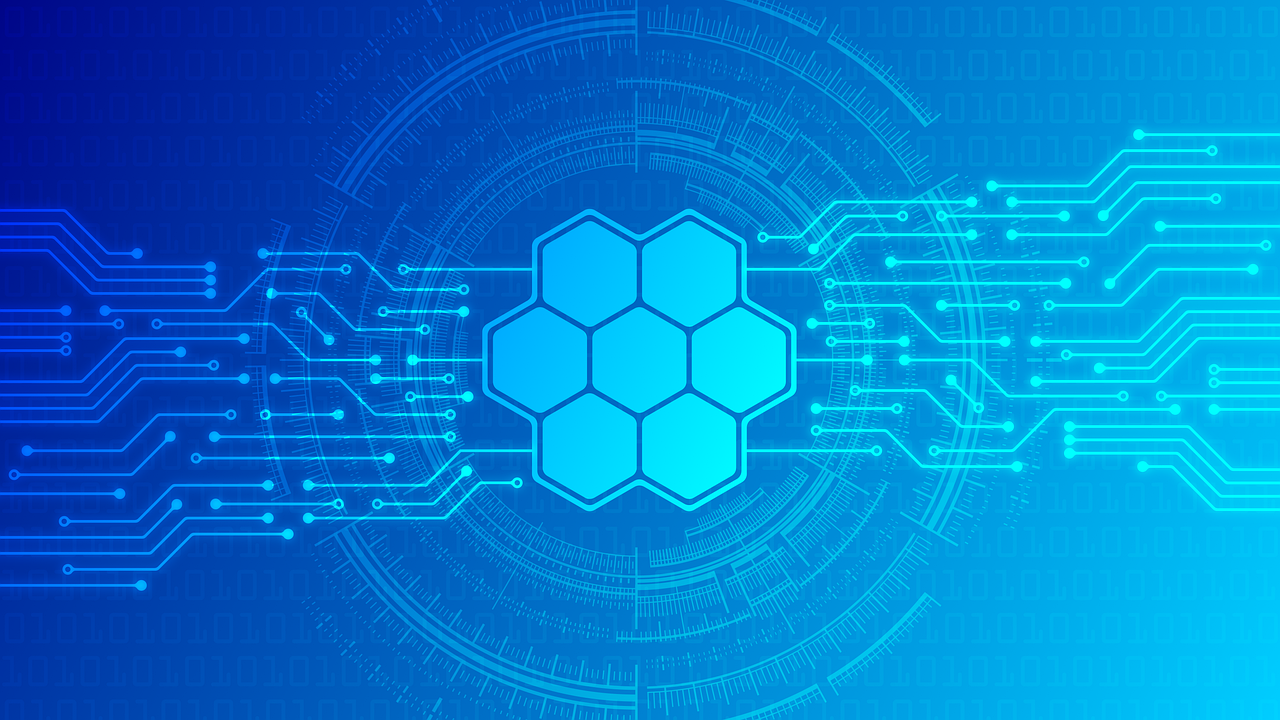
TECH TALK
High Reliability Insights From ES Components
The Official Blog of
What Are Electronic Component Packaged Devices or Integrated Circuit Packaging?
In very simple terms, Packaged Devices is nothing more than an encasement that surrounds the circuit device to protect it from physical impairment or corrosion. In addition, it also allows electrical contacts that are mounted on the device to connect to a printed circuit board.
Reference: Wikipedia
In very simple terms, Packaged Devices is nothing more than an encasement that surrounds the circuit device to protect it from physical impairment or corrosion. In addition, it also allows electrical contacts that are mounted on the device to connect to a printed circuit board
Short History: Early 1970’s through early 2000’s.
So how did all this stuff start with Packaged Devices? The earliest integrated circuits were packaged in what are called “Ceramic Flat Packs”. These were a
Military standardized printed circuit board surface mount component packages or “Flat Packs” The other type of packaging used in the 1970s, was called the
ICP (Integrated Circuit Package). After that, these “Packaged Devices” kept evolving as technology advanced. Commercial circuit packaging quickly moved to
DIP or Dual-In-Line Packaging made from ceramic and then later plastic.
Next came PGA or Pin-Grid Array and LCC, Leadless Chip Carrier. After that, Surface Mount Packaging appeared to be the next new thing. The electrical components could be mounted directly onto the surface of the printed circuit board. Then came the Small Outline Integrated Circuit that occupied an area about 30-50% less than the Dual In-Line Packaging.
Next was the area array package, that was a ceramic Pin Grid Array Package
Then there was the Ball Grid Array or BGA. but evolved into Flip-Chip Ball Grid Array (FCBGA) packages in the 1990s. FCBGA packages allow for much higher pin count than any existing package types. In an FCBGA package, the die is mounted upside-down (flipped) and connects to the package balls via a substrate that is similar to a printed-circuit board rather than by wires. FCBGA packages allow an array of input-output signals (called Area-I/O) to be distributed over the entire die rather than being confined to the die periphery.
OPERATION PROPERTIES: (DIE)
Traces out of the die, through the package, and into the printed circuit board have very different electrical properties, compared to on-chip signals. They require special design techniques and need much more electric power than signals confined to the chip itself.
Recent developments consist of stacking multiple dies in single package called SiP, for System In Package, or three-dimensional integrated circuit. Combining multiple dies on a small substrate, often ceramic, is called an MCM, or Multi-Chip Module. The boundary between a big MCM and a small printed circuit board is sometimes blurry.
WHAT DOES THIS ALL MEAN TO A “NON-ENGINEER?”
Well, to help you when you are searching for these devices, here are some common Package Types and images of these Packaged Devices.
Are you soldering to the top contact or wire bonding?
This is a must if there are any power discrete devices on the BOM. Many discrete die are available with either option. The rest are only offered with one or the other of these two options. If only solderable top metal is available, and there are no alternative devices, the die distributor can possibly offer a sub-assembly using a Copper or Molybdenum disk with suitable top plating to meet wire bond requirements.
How are you planning to attach the die?
The vast majority of power discretes are available from the manufacturer with solderable back metal only, some with either solderable or gold back metal. If the user is planning to use epoxy attach, it is highly recommended that they not use die with solderable metals. Gold back metal is recommended for either eutectic or epoxy attach. At ES Components we have developed and qualified the ability to remove solderable back metal from wafers and deposit gold for devices where this option is not available from the vendor. Silicon back die are generally epoxy-attached and if a eutectic attach is required, a gold alloy preform is needed.
How will you want this bare die packaged for delivery in full production?
Packaged parts are typically supplied in production quantities on tape-and-reel with nearly infinite shelf life. Waffle packs are the most common medium for shipping bare die, but high volume automatic assemblies are moving towards sawn wafer on film to reduce cost and enhance manufacturing throughput. However, sawn wafer on film has shelf life limitations which demand special management of the supply pipeline. A die distributor can manage the pipeline so that probed unsawn wafers are kept in stock in the appropriate environment and sawn wafers on film are limited to only those wafers needed for short-term production. If there is a delay in manufacturing, the unsawn wafer inventory remains pristine and the shelf life issue is confined to a small subset of the inventory.
Summary
By answering these questions at the time of initial contact and early in the design process, it’s possible to save the user time and money by avoiding the need to modify or redesign the function based on sample evaluation possibly weeks or even months later. We can also properly code the die part number to capture all the pertinent information for future reference.